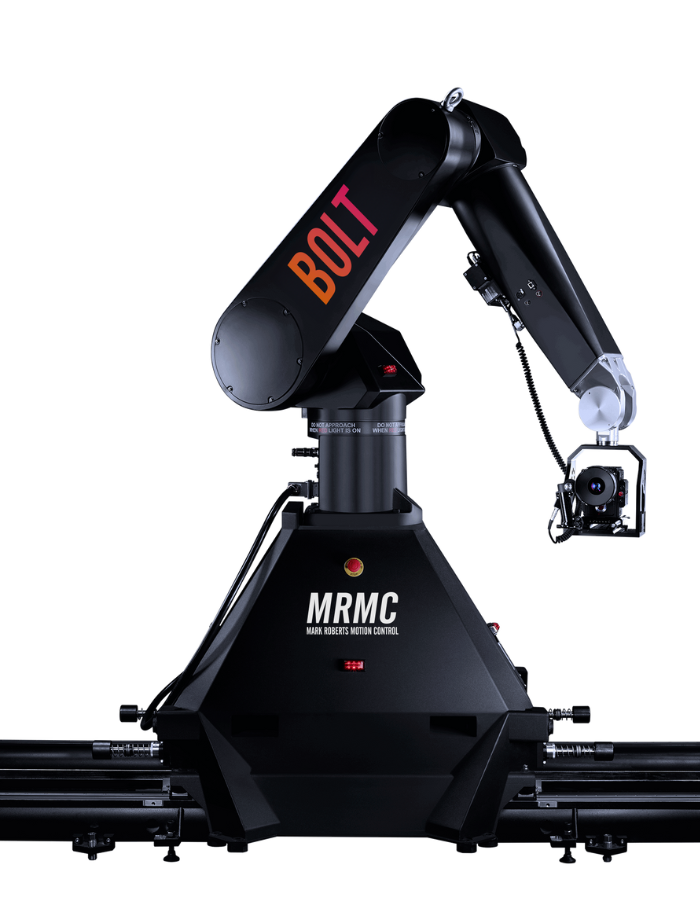
Bolt
HIGH SPEED CAMERA ROBOT
The Bolt™ High-Speed Cinebot is the ultimate all-in-one package for high-speed filming – capturing footage in crisp focus that would be impossible by hand or any other method. This precision camera robot adds an entirely new perspective to your production – whether shooting commercials, tabletop work, film or TV.
The Bolt™ High-Speed Cinebot is the ultimate all-in-one package for high-speed filming – capturing footage in crisp focus that would be impossible by hand or any other method. This precision camera robot adds an entirely new perspective to your production – whether shooting commercials, tabletop work, film or TV.
HIGH-SPEED CINEMA ROBOT FEATURES
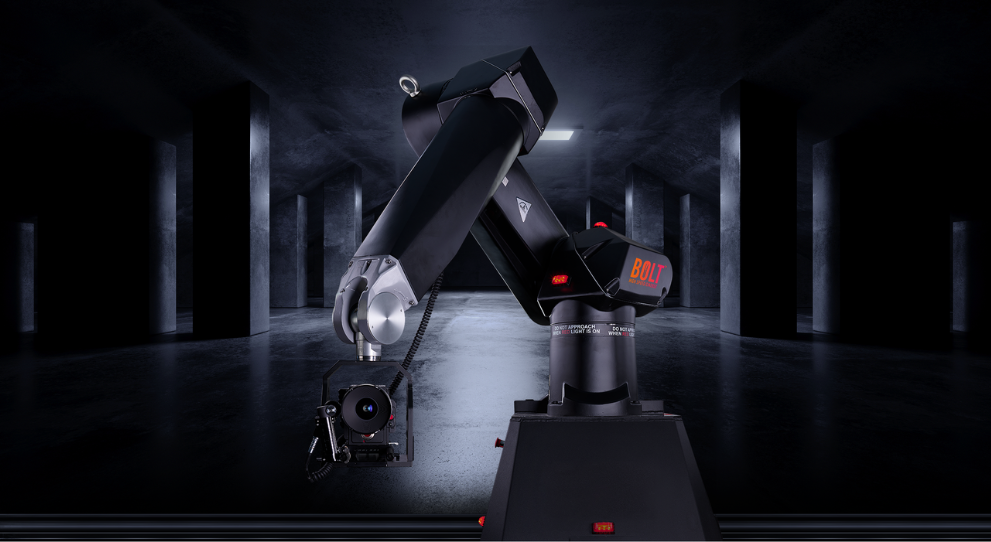
PRECISION CINEMA ROBOT
The Bolt can move from standstill to full high-speed motion and back to a complete stop in fractions of a second – perfect for capturing fast-paced action and slow motion footage with pinpoint accuracy. The precision robotic arm is capable of moving at up to 12 metres per second when combined with track, and at 180-degrees of rotation in 1 second. In summary, the Bolt cinema robot can keep up with just about anything!
The Bolt can move from standstill to full high-speed motion and back to a complete stop in fractions of a second – perfect for capturing fast-paced action and slow motion footage with pinpoint accuracy. The precision robotic arm is capable of moving at up to 12 metres per second when combined with track, and at 180-degrees of rotation in 1 second. In summary, the Bolt cinema robot can keep up with just about anything!
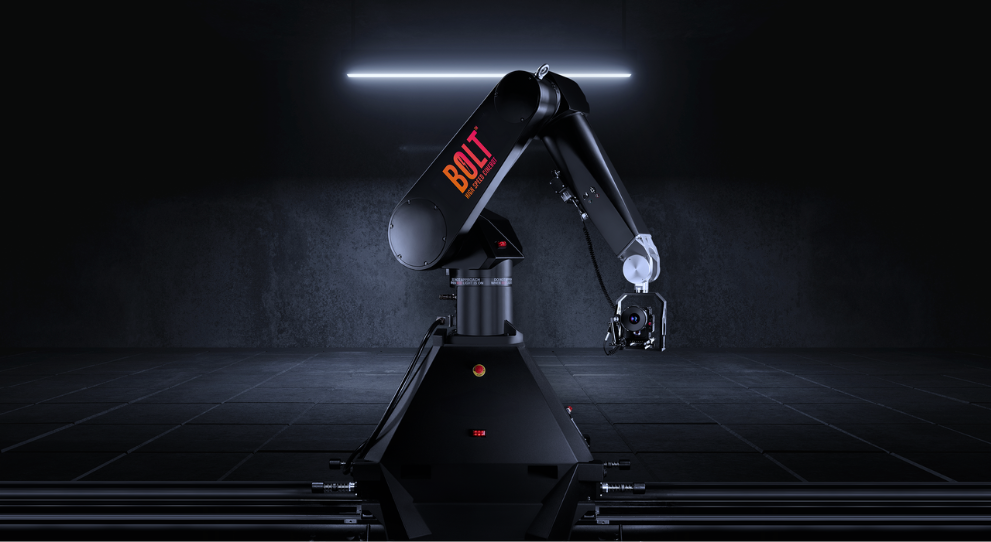
high-speed automated image capture
- High-speed precision camera robot
- 6 axis robotic arm
- Camera payload up to 20kg
- Track speeds up to 5m/sec
- Arm reach 2m
- Max Height 3.5m
- Can be used as model mover
- Perfect for live-action or tabletop shoots
- For a longer reach high-speed cinema robot look at Bolt X
- For a small high-speed rig look at the Bolt Jr+
- High-speed precision camera robot
- 6 axis robotic arm
- Camera payload up to 20kg
- Track speeds up to 5m/sec
- Arm reach 2m
- Max Height 3.5m
- Can be used as model mover
- Perfect for live-action or tabletop shoots
- For a longer reach high-speed cinema robot look at Bolt X
- For a small high-speed rig look at the Bolt Jr+
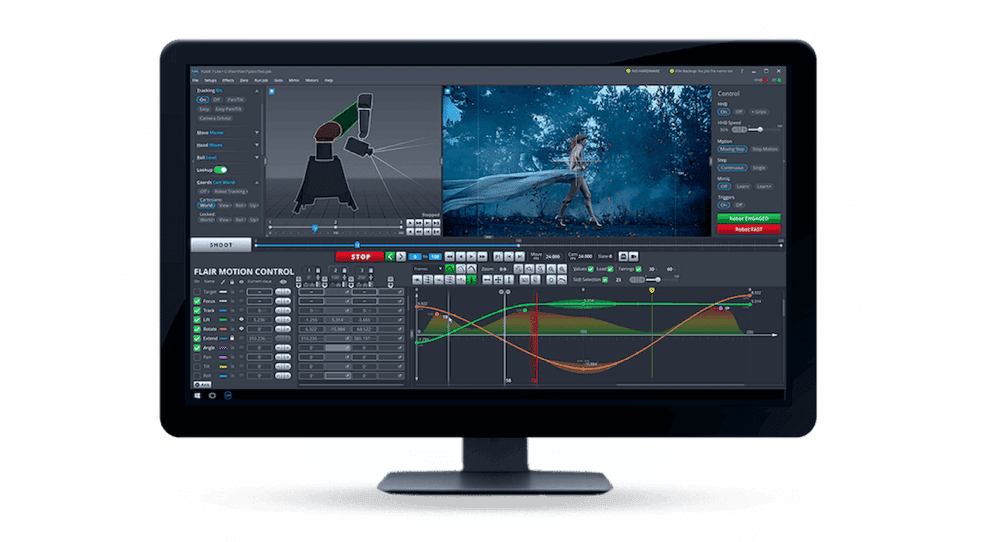
Industry Standard Software
Flair is MRMC’s premier motion control software
Designed to give exceptional command over camera movement, Flair precisely controls up to 500 axes of motion and interfaces seamlessly with CGI packages such as Unreal Engine. Flair is the tool that makes your vision reality.
Designed to give exceptional command over camera movement, Flair precisely controls up to 500 axes of motion and interfaces seamlessly with CGI packages such as Unreal Engine. Flair is the tool that makes your vision reality.
Feature Highlights
Bolt PTR Robotic Head
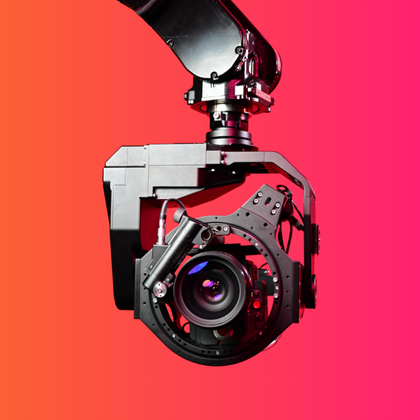
Upgrade Your Setup
Take your motion control to the next level with the Bolt PTR (Pan-Tilt-Roll) Robotic Head — a high-precision, compact camera head designed for the Bolt and Bolt X Cinebots.
The Bolt PTR allows your camera to pan, tilt, and roll independently of the Bolt arm, giving you total control over your shots and greater freedom of movement. It’s perfect for confined spaces like car interiors or miniature sets.
Featuring a precision-engineered servo motor and gearbox, the Bolt PTR brings smoother, more stable, and highly responsive performance to your Bolt system, no matter the shot.
Track Options
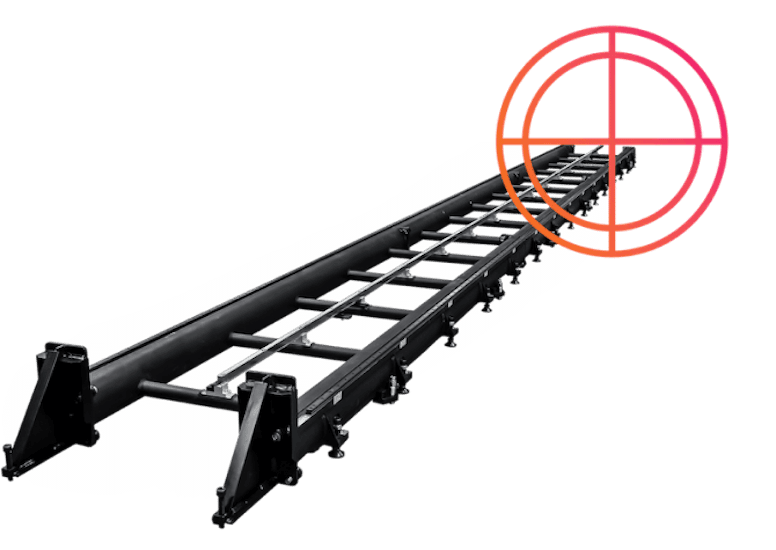
BOLT CINEMA ROBOT ON TRACK
To add a 7th axis of movement, you can run the Bolt on track. This setup allows it to seamlessly follow any object, person, or landscape, ensuring your subject stays in frame no matter how far they move. With an unlimited track length and speeds of up to 12 meters per second with combined arm movement, the Bolt delivers unparalleled flexibility for all your shooting needs, setting a new standard for dynamic high-speed camera tracking shots.
Specifications
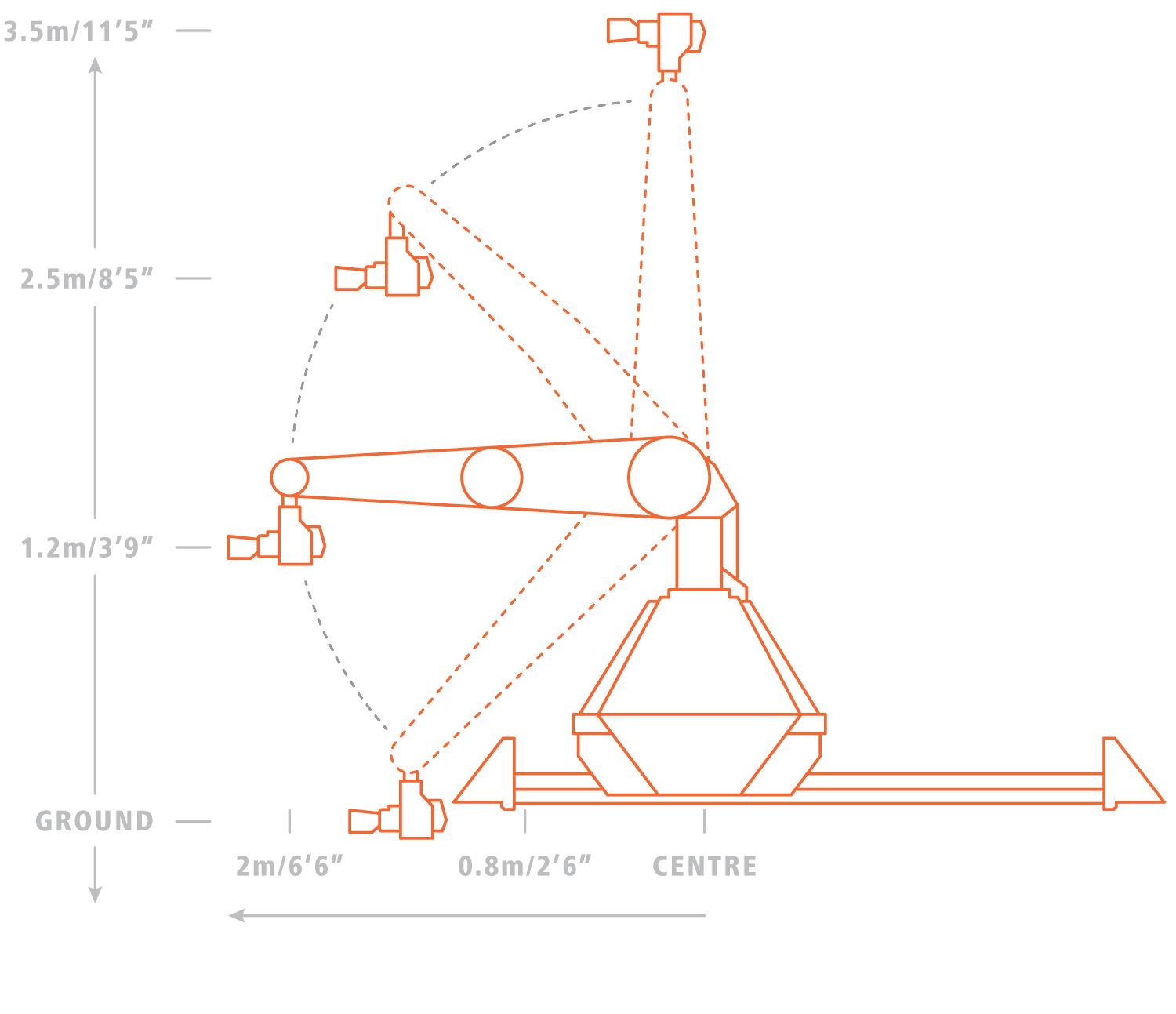
Operating envelope
Max Height (from ground)
3.5m / 11'5"
Max Reach (from rotate centre)
2.0m / 6'6"
Lowest Position
0m / 0'
Rig Performance
Arm ARC Move
7 m/s max speed at camera
Arm with Track
12 m/s max speed at camera
Track
5 m/s max speed at camera
Rotate
-160˚ to+160˚ range of travel @ 240˚/s
Lift
-40˚ to +210˚ range of travel @ 240˚/s
Arm
-60˚ to +220˚ range of travel @ 300˚/s
Pan
-265˚ to +265˚ range of travel @ 350˚/s
Tilt
-210˚ to +10˚ range of travel @ 350˚/s
Roll
-720˚ to +720˚ range of travel @ 870˚/s
Practical Shooting Speeds
Vertical
1m (3’3”) vertical movement /0.5s
Horizontal
1m (3’3”) horizontal movement /0.5
Arc
Complete 180˚ arc with 75cm (2’5”) radius /1.5s Complete 180˚ arc with 45cm (2’5”) radius /1s
Rig Weights
Bolt + Base
600kg / 1323lbs
Maximum camera payload
20kg / 44lbs
Power Connection
Power Requirements
3x 400 volts, 32 amps, 50-60Hz
Generator
3k VA (Bolt™) 14k VA (Bolt™ on track)
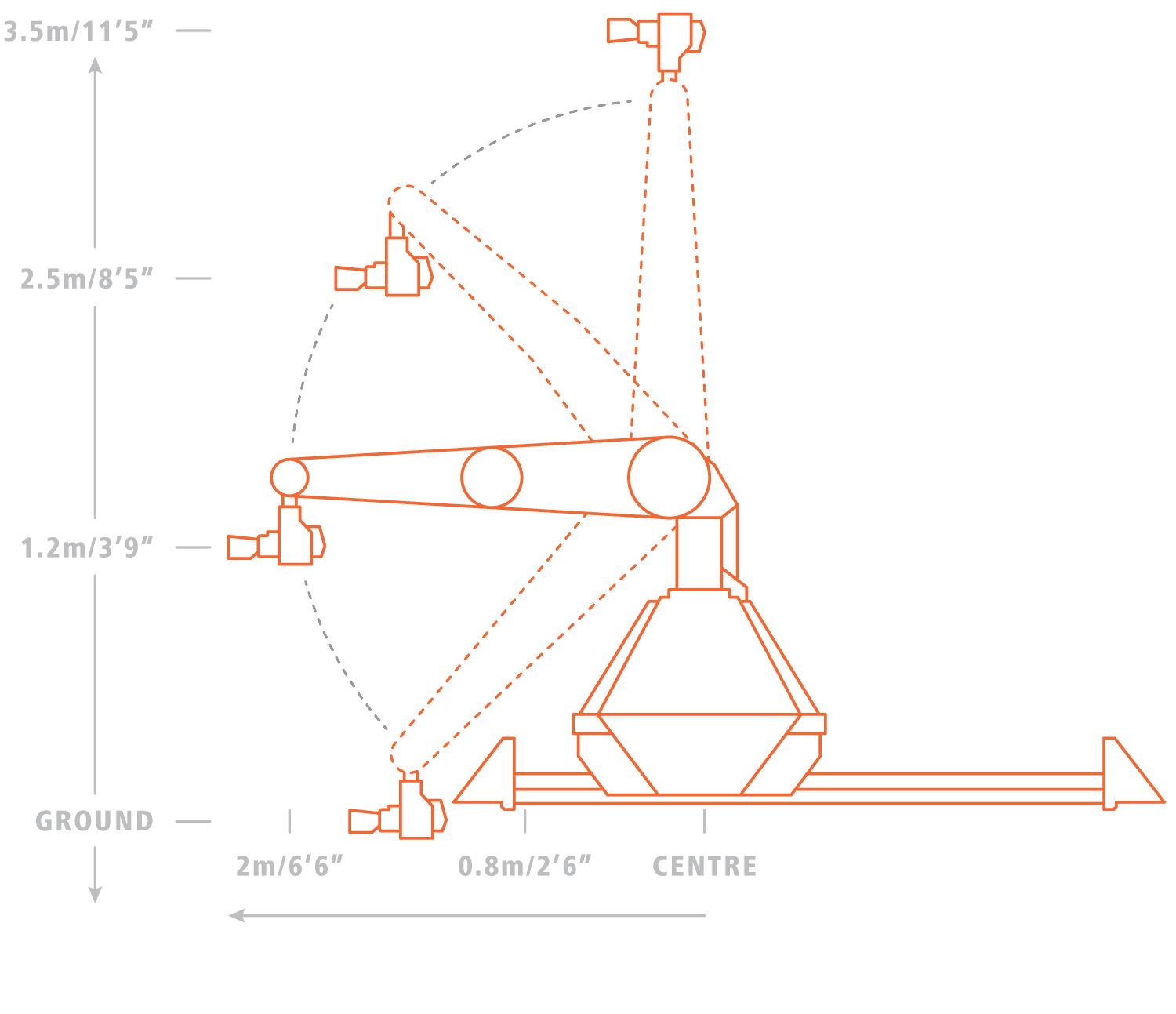
Controllers
Accessories
Videos

Motion Control Robotics Summer Showreel — June.2024

High Speed Motion Control Robotics Spring Showreel— April.2023

High-Speed Winter Showreel — Dec.2022

High-Speed Cinebot Showreel — Sept.2022

High-Speed Cinebot Showreel —Jan. 2022
